ToolingIQ: Your Key To Eliminate Costly Downtime Now!
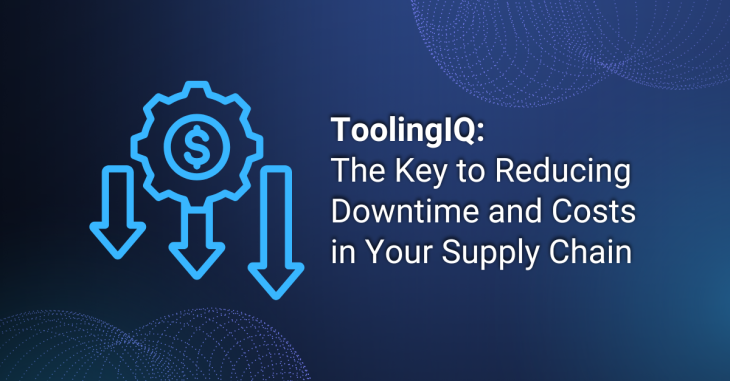
Tooling plays a crucial role in manufacturing but managing it can be complex. Tooling is often custom-made, expensive, and located at supplier sites. This increases the risks of delays, unplanned costs, and compromised product quality. Without proper oversight, these challenges can negatively impact supply chain efficiency. To solve these issues, Rhythm Innovations has created ToolingIQ—a cloud-based solution designed to optimize the lifecycle of tooling assets across your supply chain.
Overcoming Tooling Challenges with ToolingIQ
ToolingIQ offers features that help companies avoid unnecessary downtime, reduce costs, and keep tools ready for production. Here’s how it addresses common tooling challenges:
Key Features and Benefits of ToolingIQ
- Real-Time Visibility: ToolingIQ provides instant access to the location, condition, and lifecycle of tooling assets. With real-time monitoring, businesses can make decisions that prevent disruptions and keep production on track.
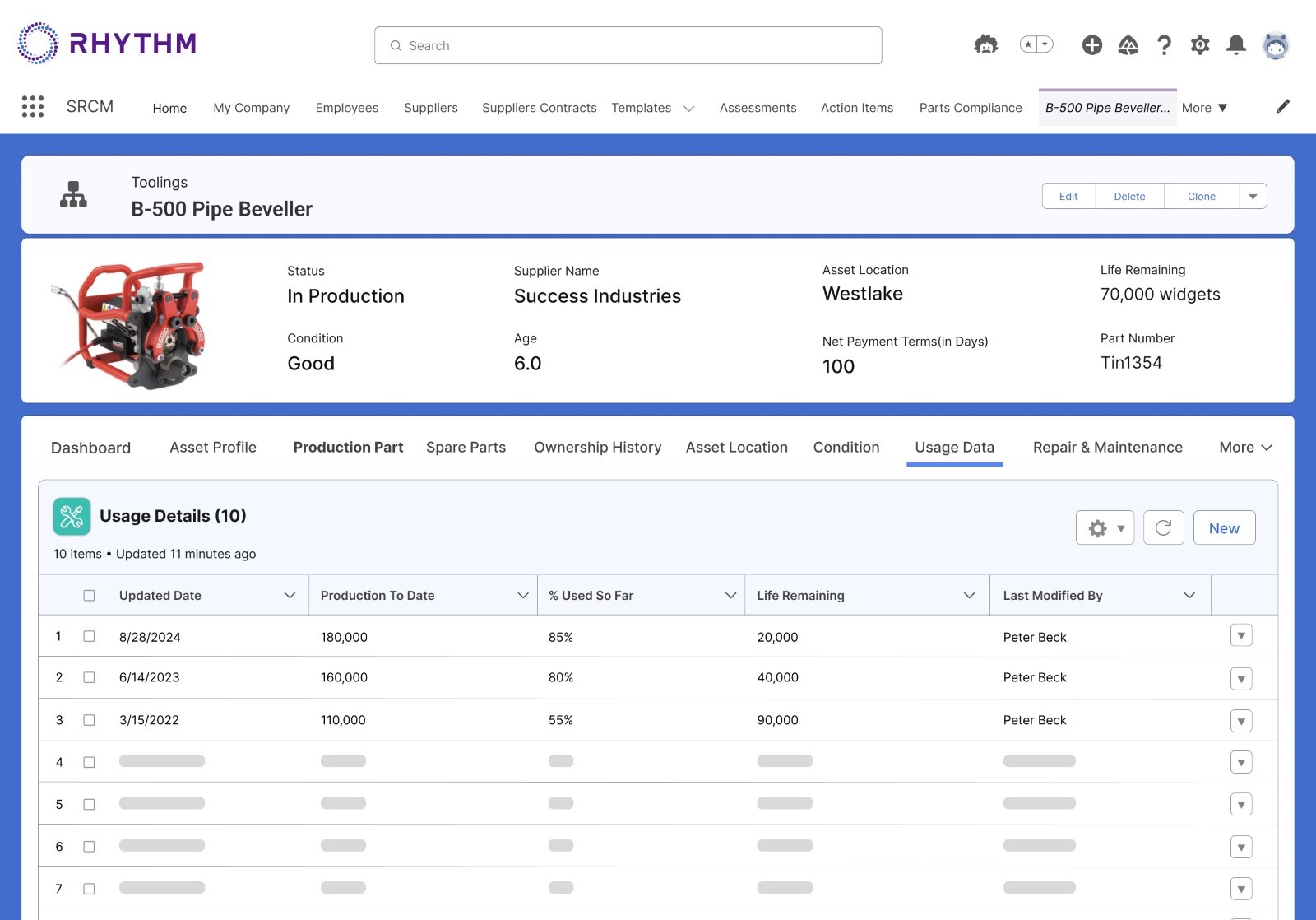
- Proactive Supplier Collaboration: ToolingIQ creates a centralized system that monitors tooling conditions and tracks performance. This proactive approach helps both suppliers and manufacturers work together more efficiently.
- Track Remaining Useful Life with Precision: By capturing usage data, wear patterns, and maintenance history, ToolingIQ provides accurate insights into how much life is left in each tool. This helps with timely budget planning, preventing unexpected capital expenditure demands.
- Analytics-Driven Insights: ToolingIQ provides data-driven insights into tool performance, helping identify areas for improvement. It forecasts potential failures and optimizes usage, allowing businesses to reduce costs.
- Eliminate Downtime Risks: ToolingIQ forecasts potential tooling failures and helps you plan repairs or replacements. By reducing downtime, companies can keep production running smoothly and avoid costly delays.
- Seamless Integration: ToolingIQ integrates smoothly with ERP/MRP and MES systems. This helps consolidate tooling data, improve production planning, and enhance collaboration across departments.
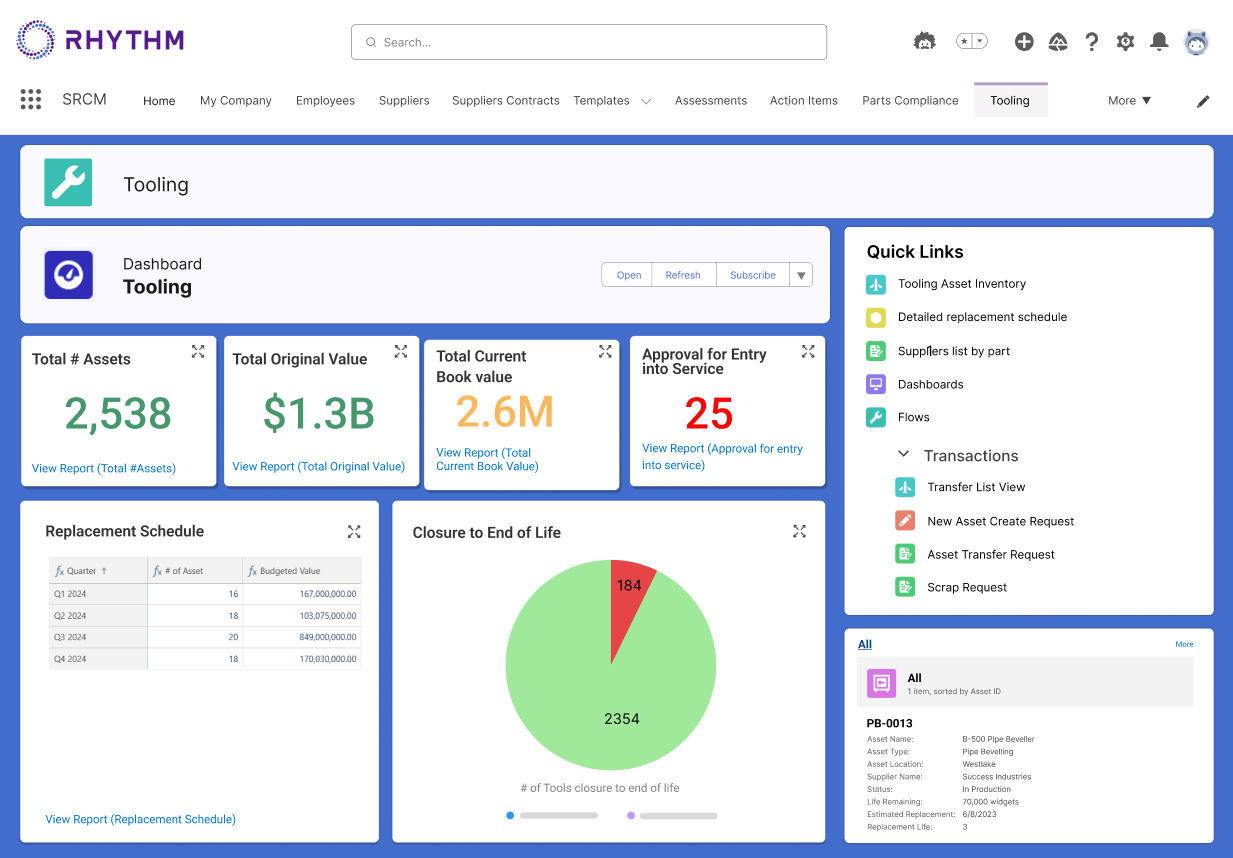
Why ToolingIQ is a Game-Changer
ToolingIQ helps businesses avoid challenges that can disrupt production. A combination of real-time monitoring, predictive analytics, and seamless integration boosts supply chain efficiency.
Take Control of Your Tooling Assets Today
Transform your supply chain operations with ToolingIQ. With real-time visibility and optimization, ToolingIQ helps reduce costs and prevent disruptions. Take charge of your tooling management and improve your processes.
Ready to elevate your tooling management? Visit Rhythm Innovations to learn more or schedule a demo.